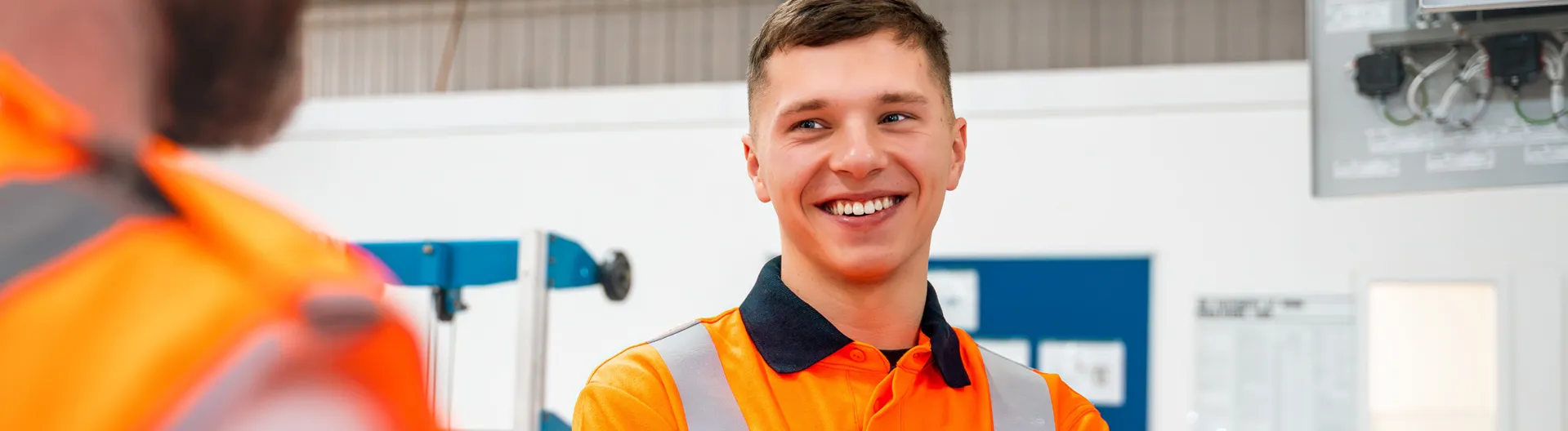
Engineering Manufacturing Technician Higher Apprenticeship Standard
Course Code: NRT534Z
Course Level: Level 4
Study Mode: Apprenticeship
Course Type: Apprenticeships
Course overview
This apprenticeship focuses on developing advanced engineering skills, including designing, testing and manufacturing products, preparing apprentices for technical roles in engineering companies.
The topics you will cover whilst training include: BTEC Higher National Certificate in Engineering Level 4.
Typical job roles include: Manufacturing engineer quality, Manufacturing production engineer, Manufacturing procurement engineer, Quality engineer, Costing engineer, Test and commissioning engineer, Installation engineer, Process engineer, Production support engineer.
Engineering Manufacturing Technicians can be office based, manufacturing/plant based or more commonly combination of both, working with engineering and/or manufacturing teams at an operational level such as with production team leaders and/or management level working with specialist quality or design engineers.
The broad purpose of the occupation is to provide specialist technical support for engineers, so that organisations can develop, produce or test new/existing products, processes, or procedures to meet a customer specification in terms of quality, cost and delivery, as efficiently and effectively as possible.
Engineering Manufacturing Technicians gather information and data from a range of sources and analyse the information/data. They will make decisions, solve problems and produce and/or update technical documentation, reports or specifications covering areas such as quality, reliability, production schedules/targets, costing or other technical documentation that informs others, either internally or externally what needs to be done such as how a product must be designed, manufactured, tested, modified, maintained, stored, transported, commissioned or decommissioned.
In their daily work, an employee in this occupation interacts with their line manager to confirm departmental programmes of work and to agree individual responsibilities. This in turn will align to an overarching organisational resource and delivery plan. As well as liaising with internal colleagues, they may also be responsible for working directly with customers and/or suppliers or with representatives from appropriate regulatory bodies. Typically this would involve interaction with auditors to demonstrate compliance to specific organisational or regulatory requirements (such as Civil Aviation Authority).Their time will be spent between working in an office environment and working in the manufacturing environment or visiting customers or suppliers as and when required.
An employee in this occupation will be responsible for the quality, safety and delivery of the manufactured product or service, ensuring it is delivered to the customer on time at the agreed cost. They will typically report to an engineering or manufacturing manager as part of a cross functional team, the size of this team and responsibilities will vary depending on the size of the employer. Although working within defined quality processes and procedures, they are responsible for the delivery, quality and accuracy of the work they complete. They have the autonomy to use judgement when undertaking the occupational duties and applying their technical knowledge, skills and behaviours in a wide range of contexts and environments. They use a range of tools and techniques to support decision making and solve problems that are often complex and non-routine. They also have a responsibility to identify and contribute to making improvements such as business processes, procedures, ways and methods of working.
In order to optimise success candidates will typically have 5 GCSE's at Grade C (Grade 4/5 in the new numerical GCSE grading system) or above, including Mathematics, English and a Science, Technology or Engineering related subject, and 90+ credits in Engineering at level 3. *(As further guidance, the level of Mathematics has an advisory GCSE level of grade B (Grade 5/6 in the new numerical GCSE grading system)
Your progress is continually monitored throughout the course. Assessments are arranged when necessary and these take place on-the-job.
Together with the college day release courses, which would be over 36 - 42 months.
Assessments will include:
By observing of your performance; responses to written and/or spoken questions to show your knowledge and understanding; e-portfolio of supporting evidence containing testimonies, reflective accounts, assignments, work products such as activity planning sheets, completed risk assessments, continual professional development evidence.
Once you have completed your programme, met all of the pre-requisites for the EPA, including English and maths requirements, and your employer is satisfied that you are consistently working at or above the level set out in the occupational standard, you will be put through for your End Point Assessment which will take place within a 3 month EPA period.
The EPA consists of 2 assessment methods:
- Practical observation with questioning
- Professional discussion underpinned by portfolio of evidence
Email: apprenticeships@nscg.ac.uk
1 of 13
DfE Expert Training Providers
Results 13%
above national average